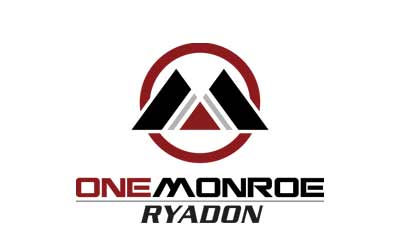
In the manufacturing sector, casting technologies are widely utilized to create goods and components with intricate shapes. Although there are many alternative casting techniques, the most entail pouring a liquid substance into the center of a hollow mold, such as hot plastic or molten metal. The liquid substance is removed from the mold’s cavity after it has cooled. Having said that, investment casting is a distinctive casting technique that has grown in popularity recently.
Introduction to Investment Casting
Lost-wax casting is the foundation of investment casting, a centuries-old casting technique. It entails applying a liquid substance to a wax mold. The wax starts to melt off as it warms up. The cavity of the mold is then filled with molten metal, thus replacing the wax that previously filled it. Finally, the metal is allowed to cool before being detached from the mold and removed.
Because the mold design used in this casting method is “invested” with the liquid refractory material, it is known as “investment casting.” Investment casting goes a step further by encircling the mold with the liquid material, as opposed to conventional casting methods that only require pouring the liquid material into the cavity of the mold. The liquid refractory substance is “invested” into the mold during this first step.
Investment casting benefits
The advantages of investment casting are numerous and remarkable. It is possible to produce goods and components with a superior surface quality since it requires coating the mold with a liquid refractory material. Stainless steel, brass, carbon steel, aluminum, glass, and plastic are just a few of the materials that investment casting may support. Due to its low waste production compared to other casting methods, investment casting is regarded as a highly efficient process.
Issues with Investment Casting
On the other hand, investment casting has some drawbacks, one of which is its high price. Given that investing casting is more expensive than other casting techniques, some manufacturing companies might decide not to use it. It’s also important to note that extremely small or deep holes cannot be supported by investment casting. The majority of investment techniques can only produce holes deeper than 1.5 times the diameter and larger than 1.6 mm in diameter.
Most castable metal types can be used for investment casting. Having stated that, the most typical metals employed in this casting technique are copper and copper alloys. Investment casting is distinguished by coating the mold with a liquid refractory substance before filling it with the liquid material, regardless of the metal that is employed.